Production - Made in Austria
Three manufacturing areas are combined in Zell am See
Chemical production
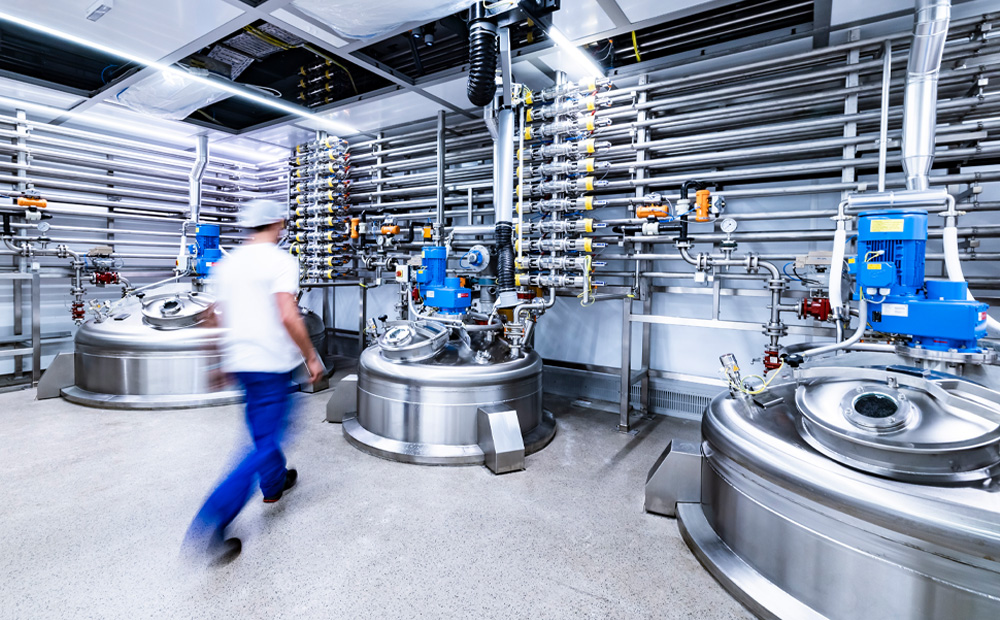
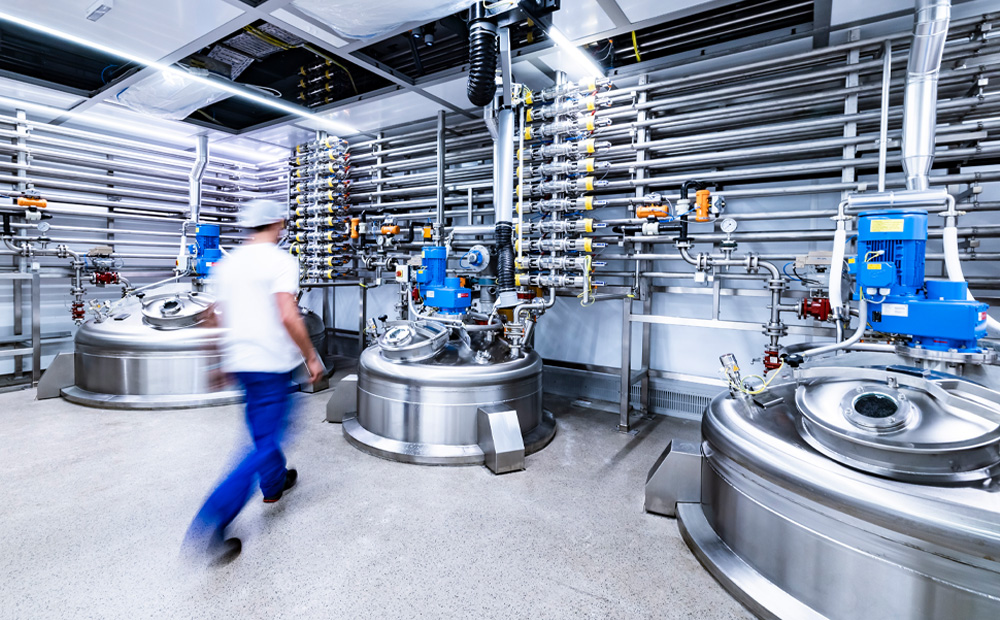
The principles of good manufacturing practice apply at the chemical plant, ensuring particularly high standards of hygiene.
Formulations and filling are both fully automated and controlled by a computer system. Containers from 30 ml to 1000 kg are filled at a rate of up to 60 bottles per minute.
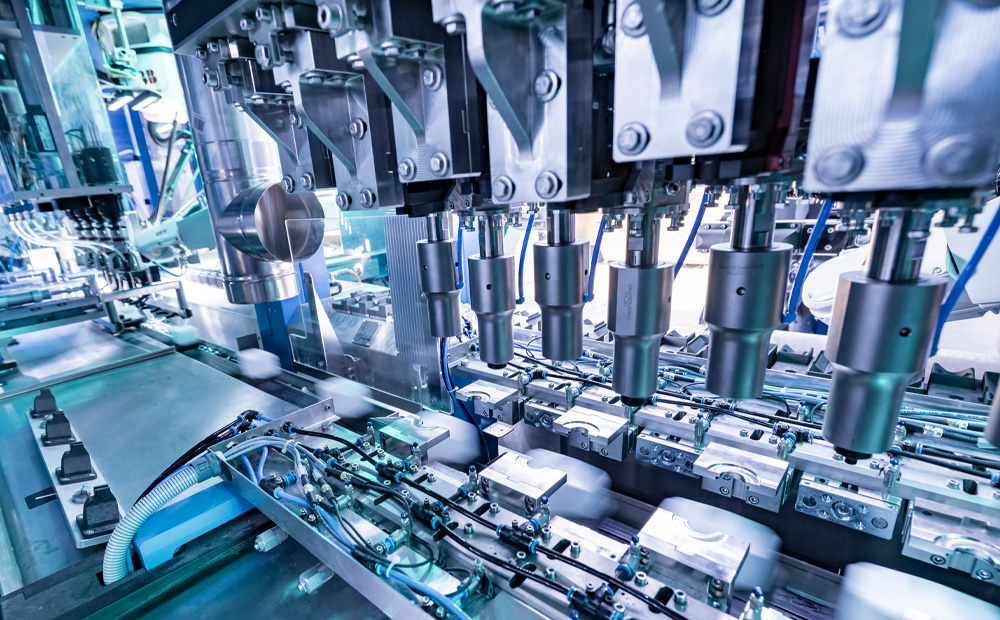
We also produce disinfecting wipes and vacuumBAGs – shrink bags that are up to 60 percent lighter than conventional soap refills, which reduce to as little as 10 percent of their original volume during consumption.
Insights into chemical production:

Production
60 bottles per minute

Shrink bags
90% less waste

Soap refills
60% lighter
Paper production
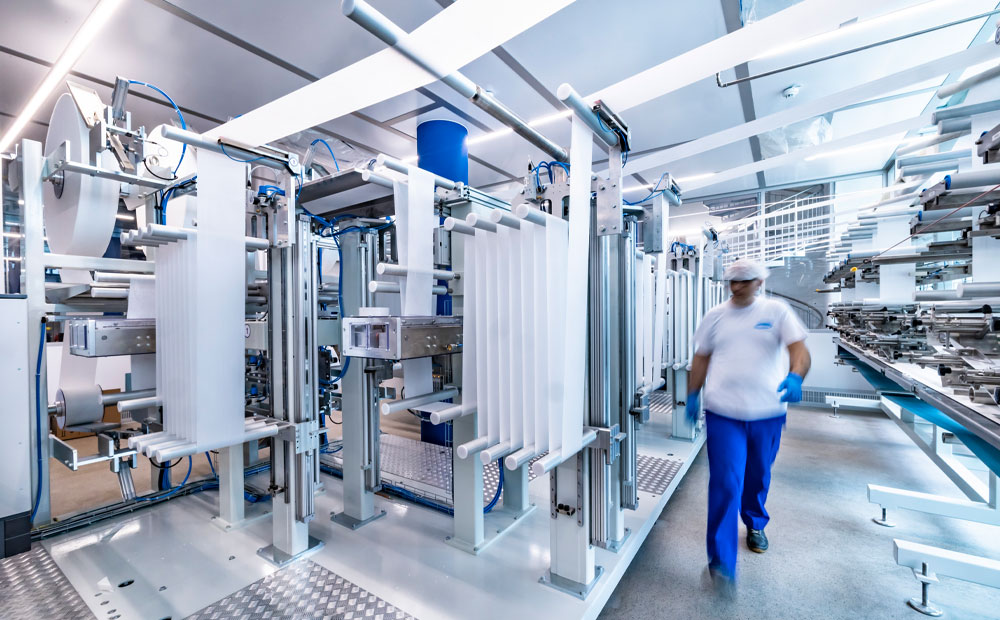
Our state-of-the-art processing lines allow for fully automated paper finishing of the highest quality.
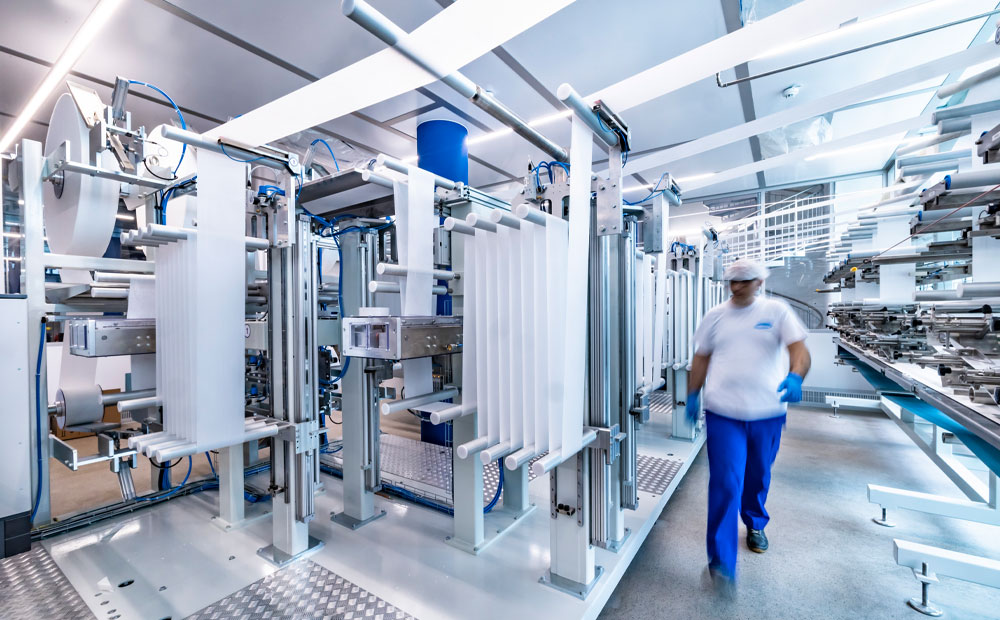
Our toilet paper and paper towels are pressed, glued, perforated, cut and then packed on our paper conversion machines.
The many certificates attesting our paper qualities verify that we pay full attention to our ecological responsibility right from the purchase of the raw material.
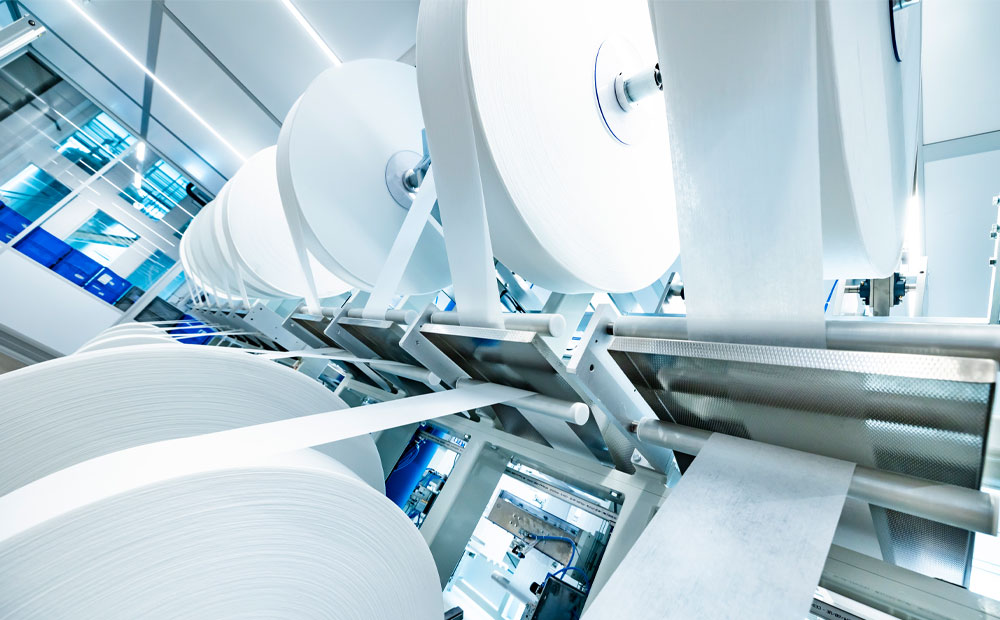
The multiROLL paper refills for the washroom and hotel room dispensers are wound compactly on narrow plastic cores. Compared to conventional paper rolls, this means up to four times more paper on the rolls. This production method not only reduces the storage volume at the customer's site, but also plays a major role in environmental protection thanks to the low transport volume.
Insights into paper production:

Paper quality
certified

Responsibility
environmentally friendly

Roll
4 times more paper
Injection moulding production
High tech comes into its own in the dispenser construction division. The devices deliver hygiene as well as data.
Hygiene means soap, paper, skin care, disinfectants, cleaners, and room fragrances;
Ddata means consumption, fill level, energy status, and service requirements.
In an area of 2,000 square metres, we’ve created the most modern dispenser manufacturing facility in the whole of Europe.
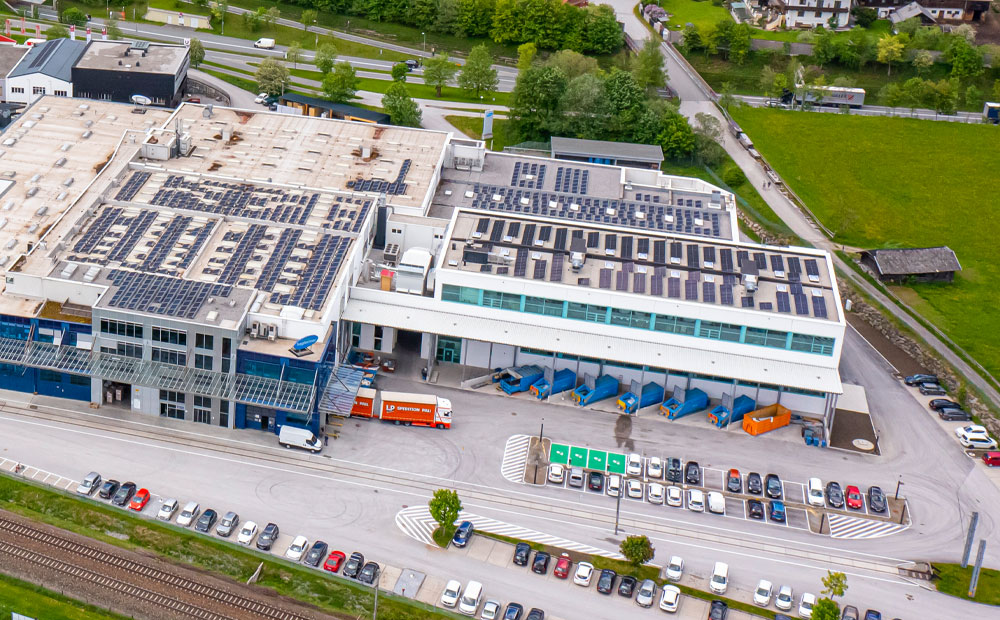
It’s now only 25 metres from the plastic granulate to the finished Hagleitner dispenser. The individual dispenser parts are produced by injection moulding on 29 injection moulding machines.
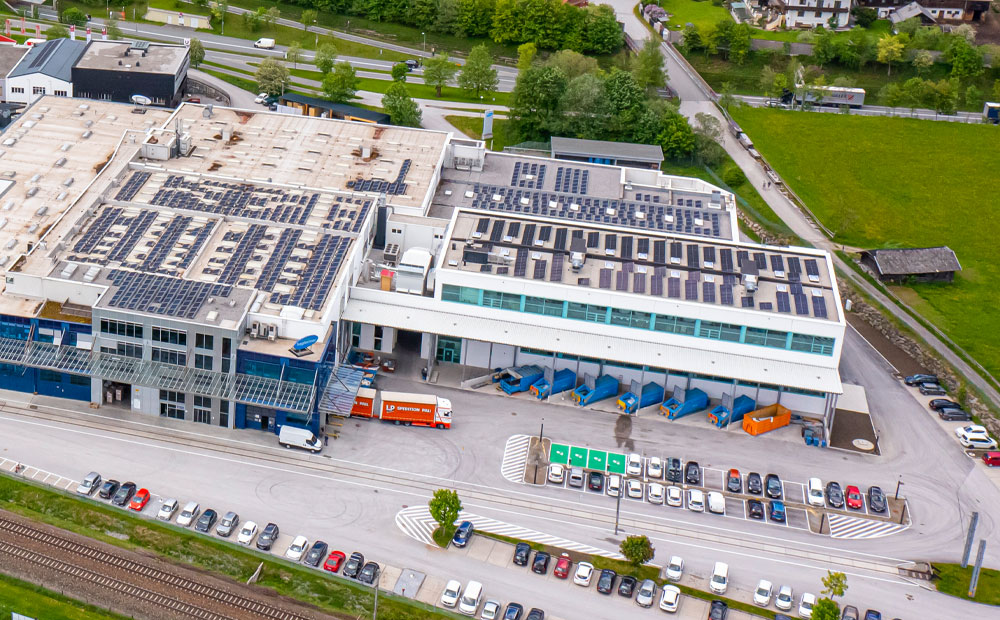
In dispenser assembly next door, colleagues work in a one-piece flow system.
This ensures the highest quality in the finished products.
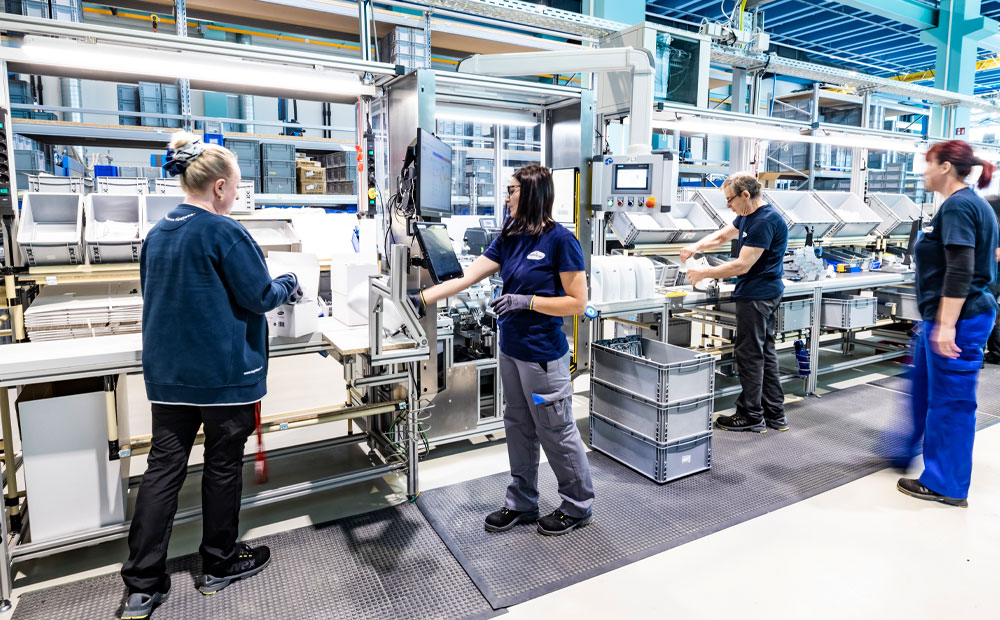
The fact that Hagleitner produces everything itself, from development to individual part manufacture through to the complete dispenser, makes the dispenser systems unbeatable.
Insights into injection moulding production:

25-metre distance
granulate > dispenser

Dispenser construction
on 2,000 square meters

Production
29 injection moulding machines

Production at Hagleitner
We are a family-run company in its third generation.
Automation and process optimisation play a key role in our production.
These greatly improve cooperation between people and machines.
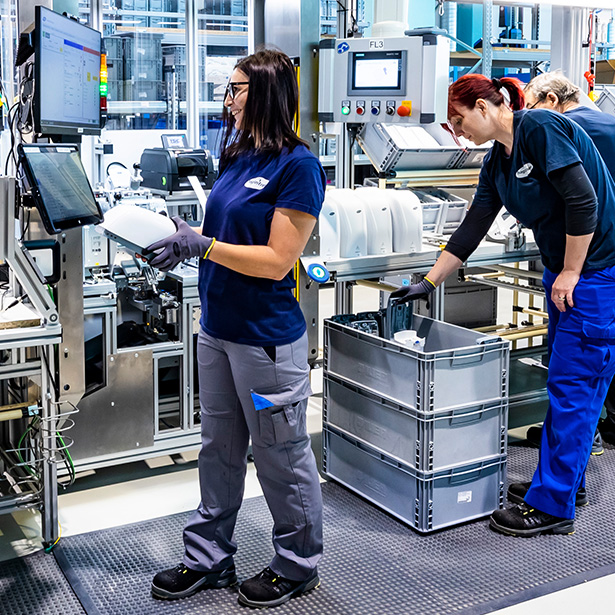